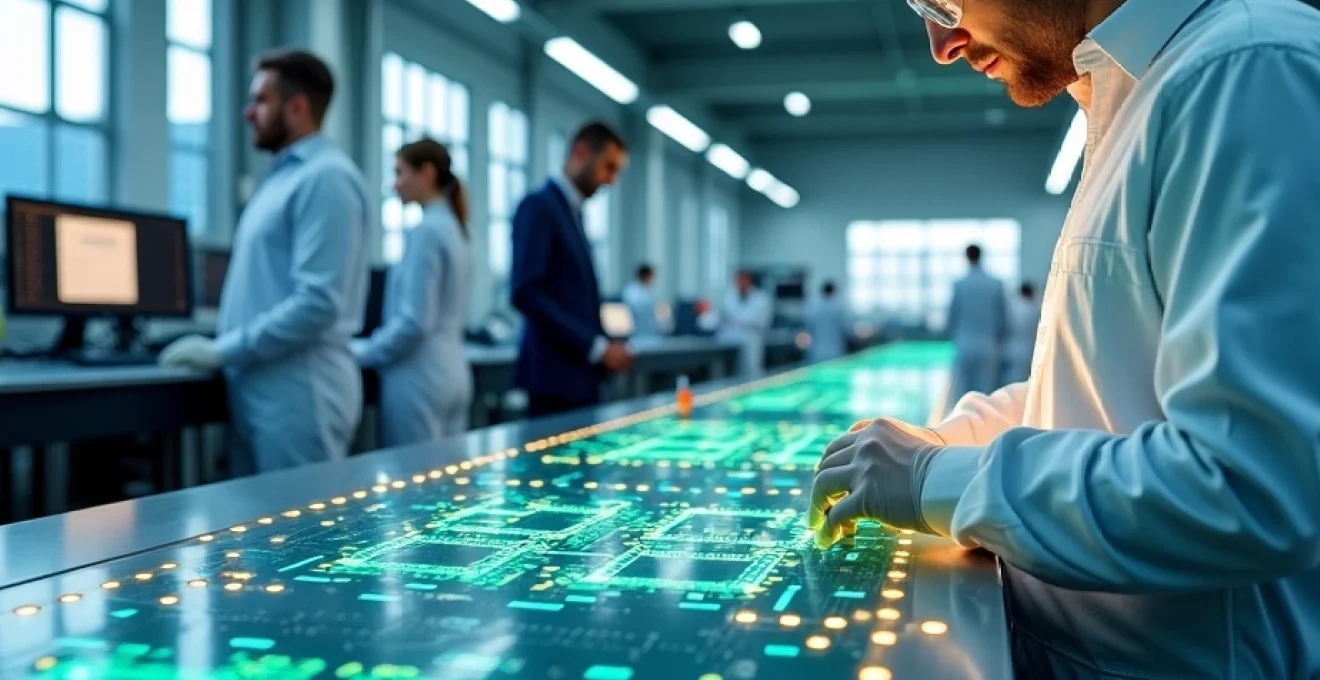
Die Leiterplattenindustrie befindet sich in einem rasanten Wandel. Mit der zunehmenden Miniaturisierung elektronischer Geräte und der Verdichtung ihrer Funktionalitäten steigen die Anforderungen an Leiterplatten kontinuierlich. Führende Hersteller treibenden technologischen Fortschritt voran und entwickeln ständig neue Methoden, um komplexere und leistungsfähigere Schaltungen auf immer kleinerem Raum zu realisieren. Diese Innovationen umfassen fortschrittliche Materialien, revolutionäre Fertigungstechniken und zukunftsweisende Designkonzepte – von Hochgeschwindigkeits-PCBs für 5G-Anwendungen bis hin zu flexiblen Leiterplatten für tragbare Elektronik.
Der Markt für Leiterplatten ist global und hart umkämpft. Deutsche und europäische Hersteller setzen dabei auf Qualität, Innovation und Spezialisierung, um gegen die asiatische Konkurrenz zu bestehen. Durch Investitionen in modernste Fertigungsanlagen, automatisierte Qualitätssicherung und umweltfreundliche Produktionsprozesse positionieren sie sich erfolgreich im Premiumsegment. Besonders in anspruchsvollen Branchen wie der Automobil-, Medizin- oder Luftfahrttechnik bieten sie maßgeschneiderte Lösungen mit höchsten Qualitätsstandards.
Technologietrends der Leiterplattenproduktion: Von Rigid-Flex bis HDI-Technik
Die Entwicklung moderner Elektronik wäre ohne fortschrittliche Leiterplattentechnologien undenkbar. Aktuelle Trends zeigen eine klare Bewegung hin zu komplexeren Board-Designs, die mehr Funktionalität auf kleinerem Raum ermöglichen. Im Zentrum stehen dabei HDI-Leiterplatten (High Density Interconnect), Rigid-Flex-Kombinationen und Spezialsubstrate für Hochfrequenzanwendungen. Diese technologien für Leiterplatten und elektronische Komponenten ermöglichen erst die fortschreitende Miniaturisierung bei gleichzeitiger Leistungssteigerung moderner Elektronikprodukte.
Die Nachfrage nach diesen fortschrittlichen Technologien wächst exponentiell. Laut aktuellen Marktanalysen wird der globale HDI-Leiterplattenmarkt bis 2026 ein Volumen von über 22 Milliarden Dollar erreichen, mit einer jährlichen Wachstumsrate von mehr als 8%. Dieser Trend wird maßgeblich durch die steigende Komplexität mobiler Geräte, Wearables und IoT-Anwendungen getrieben, die immer kompaktere und leistungsfähigere Elektronikkomponenten erfordern.
Miniaturisierung durch Advanced HDI-Leiterplatten von NCAB Group und Würth Elektronik
HDI-Leiterplatten stellen die Speerspitze der Miniaturisierungstechnologie dar. Mit ihren feinen Leiterbahnen, Microvias und hochdichten Verdrahtungen ermöglichen sie die Entwicklung immer kompakterer elektronischer Geräte. Führende Hersteller wie die NCAB Group und Würth Elektronik treiben diese Technologie kontinuierlich voran. Bei HDI-Leiterplatten werden Durchkontaktierungen mit Durchmessern unter 150 μm verwendet, die mit Laser gebohrt werden. Diese sogenannten Microvias ermöglichen deutlich höhere Packungsdichten als traditionelle mechanisch gebohrte Vias.
Die neueste Generation von HDI-Leiterplatten, oft als "Advanced HDI" bezeichnet, nutzt gestapelte und versetzt angeordnete Microvias, um die Verbindungsdichte weiter zu erhöhen. Würth Elektronik bietet inzwischen HDI-Leiterplatten mit Leiterbahnbreiten von nur 50 μm und Microvias mit Durchmessern von 75 μm an. Diese Technologien sind essenziell für moderne Smartphones, kompakte Medizingeräte und andere miniaturisierte Elektronikanwendungen.
Die Zukunft der Elektronik liegt in der Miniaturisierung. Fortschrittliche HDI-Technologien sind nicht mehr nur eine Option, sondern eine Notwendigkeit für moderne elektronische Produkte, die ständig kleiner und leistungsfähiger werden müssen.
Stackaufbau bei Rigid-Flex-Leiterplatten: Erkenntnisse von Schweizer Electronic und Eurocircuits
Rigid-Flex-Leiterplatten kombinieren die Vorteile starrer und flexibler Substrate in einem einzigen Produkt. Sie bestehen aus mindestens einer flexiblen und einer starren Sektion, die während des Herstellungsprozesses dauerhaft miteinander verbunden werden. Schweizer Electronic und Eurocircuits haben in diesem Bereich bemerkenswerte Fortschritte erzielt. Der typische Stackaufbau einer Rigid-Flex-Leiterplatte umfasst flexible Polyimid-Lagen mit Kupferleiterbahnen, die zwischen starre FR4-Lagen eingebettet werden.
Eine der größten Herausforderungen bei Rigid-Flex-Leiterplatten ist die Zuverlässigkeit der Übergangsbereiche zwischen starren und flexiblen Teilen. Moderne Designs nutzen spezielle Verstärkungsmaterialien und optimierte Lagenaufbauten, um Spannungen zu minimieren und die Lebensdauer zu maximieren. Eurocircuits hat ein innovatives Fertigungsverfahren entwickelt, das die Delaminierung in diesen kritischen Bereichen deutlich reduziert und die Zuverlässigkeit bei dynamischen Biegebeanspruchungen um bis zu 40% verbessert.
PTFE- und Rogers-Materialien für Hochfrequenzanwendungen in 5G-Technologien
Mit dem Ausbau von 5G-Netzwerken steigt der Bedarf an Hochfrequenz-Leiterplatten dramatisch an. Traditionelle FR4-Materialien stoßen bei Frequenzen über 3 GHz an ihre Grenzen, was den Einsatz spezieller HF-Substrate erforderlich macht. PTFE-basierte Materialien (Polytetrafluoroethylen) und Rogers-Laminate haben sich als optimale Lösungen für diese Anwendungen etabliert. Sie zeichnen sich durch niedrige Dielektrizitätskonstanten (typischerweise Dk 2.2-3.5
) und geringe Verlustfaktoren aus.
Die Verarbeitung dieser Spezialsubstrate erfordert besonderes Know-how, das nicht alle Leiterplattenhersteller besitzen. Rogers-Materialien wie RO4350B oder RO3003 werden inzwischen häufig für 5G-Anwendungen eingesetzt, da sie eine gute Balance zwischen HF-Eigenschaften und Verarbeitbarkeit bieten. Sie ermöglichen Signalübertragungen mit geringer Dämpfung bei Frequenzen von bis zu 100 GHz, was sie ideal für moderne Kommunikationstechnologien macht.
Embedded Components: Integration von Bauteilen nach ZVEI-Standard
Die Integration von passiven und aktiven Komponenten direkt in die Leiterplatte stellt einen bedeutenden Trend dar. Diese Technologie, bekannt als "Embedded Components", ermöglicht eine drastische Reduktion des Platzbedarfs und verbessert die elektrischen Eigenschaften durch kürzere Signalwege. Der Zentralverband Elektrotechnik- und Elektronikindustrie (ZVEI) hat Standards entwickelt, die die Implementierung dieser Technologie vereinheitlichen sollen.
Typischerweise werden zunächst passive Bauteile wie Widerstände und Kondensatoren eingebettet. Die Integration erfolgt durch spezielle Vertiefungen in den inneren Lagen der Leiterplatte, in die die Komponenten platziert und anschließend mit Kupfer kontaktiert werden. Fortschrittliche Hersteller bieten inzwischen auch die Einbettung aktiver Komponenten wie ICs an. Diese Technologie reduziert die benötigte Leiterplattenfläche um bis zu 50% und verbessert gleichzeitig die Signalintegrität durch verminderte parasitäre Effekte.
Zukunftssichere Fertigung mit Industry 4.0-konformen Leiterplattenherstellern
Die vierte industrielle Revolution verändert auch die Leiterplattenproduktion grundlegend. Industrie 4.0-Konzepte wie vernetzte Fertigungssysteme, Echtzeitdatenanalyse und vorausschauende Wartung revolutionieren die Herstellungsprozesse. Leiterplattenfertiger, die frühzeitig in diese Technologien investieren, erzielen deutliche Vorteile hinsichtlich Qualität, Effizienz und Flexibilität.
Moderne Produktionsanlagen sind mit tausenden Sensoren ausgestattet, die kontinuierlich Prozessparameter überwachen und Abweichungen in Echtzeit erkennen. Die gesammelten Daten werden durch KI-Algorithmen analysiert, um Optimierungspotenziale zu identifizieren und Fertigungsprozesse automatisch anzupassen. Diese datengestützte Produktion hat bei führenden Herstellern zu einer Reduzierung der Fehlerraten um bis zu 85% und einer Steigerung der Produktivität um mehr als 30% geführt.
Digitale Zwillinge in der PCB-Produktion: Implementierungsmodelle von Siemens und KSG
Digitale Zwillinge revolutionieren die Leiterplattenfertigung, indem sie virtuelle Abbilder realer Produktionsanlagen und -prozesse schaffen. Diese detaillierten digitalen Modelle ermöglichen Simulationen, Optimierungen und Vorhersagen in einer virtuellen Umgebung, bevor Änderungen in der realen Produktion implementiert werden. Siemens und KSG Leiterplatten GmbH haben Pionierarbeit bei der Einführung dieser Technologie in der PCB-Fertigung geleistet.
Ein typischer digitaler Zwilling umfasst drei Hauptkomponenten: ein physikalisches Modell der Fertigungsanlage, ein Datenmodell mit Echtzeit-Prozessparametern und ein analytisches Modell zur Auswertung und Vorhersage. Bei KSG hat die Implementierung digitaler Zwillinge die Anlaufzeiten neuer Produkte um 40% reduziert und die Prozessstabilität signifikant verbessert. Durch kontinuierliche Simulation unterschiedlicher Produktionsszenarien können Engpässe frühzeitig erkannt und beseitigt werden.
Automatisierte Qualitätssicherung durch AOI- und AXI-Verfahren bei Zollner und Fela
Die Qualitätssicherung wird in modernen Leiterplattenwerken zunehmend durch hochautomatisierte Inspektionssysteme übernommen. AOI (Automated Optical Inspection) und AXI (Automated X-ray Inspection) ermöglichen eine 100%-Kontrolle aller produzierten Leiterplatten mit deutlich höherer Präzision als manuelle Inspektionen. Führende Hersteller wie Zollner Elektronik AG und Fela GmbH haben diese Technologien perfektioniert.
Moderne AOI-Systeme nutzen hochauflösende Kameras und fortschrittliche Bildverarbeitungsalgorithmen, um kleinste Defekte zu erkennen. Sie können Leiterbahnbreiten bis hinunter zu 30 μm überprüfen und Abweichungen von wenigen Mikrometern detektieren. AXI-Systeme ergänzen diese Technologie, indem sie auch verdeckte Fehler in Multilayer-Leiterplatten aufspüren können. Fela hat durch die Integration dieser Systeme in ihre Produktionslinien die Fehlerrate auf unter 50 DPPM (defective parts per million) reduziert – ein beeindruckender Wert, der weit unter dem Branchendurchschnitt liegt.
Materialnachverfolgung und Supply-Chain-Integration nach VDE-Richtlinien
Die lückenlose Nachverfolgung aller Materialien wird in der Leiterplattenproduktion immer wichtiger. Besonders in sicherheitskritischen Anwendungen wie der Medizintechnik oder der Automobilindustrie müssen Hersteller die Herkunft und Verarbeitung jeder Komponente dokumentieren. Der Verband der Elektrotechnik, Elektronik und Informationstechnik (VDE) hat Richtlinien entwickelt, die Standards für diese Rückverfolgbarkeit setzen.
Moderne Trackingsysteme nutzen Barcode- oder RFID-Technologien, um jede Leiterplatte während des gesamten Produktionsprozesses zu verfolgen. Jeder Fertigungsschritt, jedes verwendete Material und jede Qualitätskontrolle werden automatisch dokumentiert und in einer zentralen Datenbank gespeichert. Diese Informationen sind nicht nur für interne Qualitätssicherungsprozesse wichtig, sondern werden zunehmend auch in die Supply-Chain-Systeme der Kunden integriert, um durchgängige Transparenz zu gewährleisten.
Smart Factory-Konzepte deutscher Leiterplattenhersteller im internationalen Vergleich
Deutsche Leiterplattenhersteller haben bei der Implementierung von Smart Factory-Konzepten eine führende Position eingenommen. Im internationalen Vergleich zeichnen sich ihre Ansätze durch besonders hohe Integrationsgrade und systemische Betrachtung aus. Während viele asiatische Hersteller primär auf Automatisierung einzelner Fertigungsschritte setzen, verfolgen deutsche Unternehmen typischerweise ganzheitliche Konzepte, die den gesamten Produktionsfluss optimieren.
Ein zentrales Element deutscher Smart Factory-Ansätze ist die vertikale Integration aller Prozessebenen – von der Auftragsannahme über die Fertigung bis zur Qualitätskontrolle und Logistik. Durch MES-Systeme
(Manufacturing Execution Systems) werden alle Produktionsschritte in Echtzeit überwacht und gesteuert. Diese integrierten Systeme ermöglichen eine außergewöhnliche Flexibilität: Führende deutsche
Hersteller bieten damit eine Anpassungsfähigkeit, die besonders bei kundenspezifischen Leiterplattenprojekten mit häufigen Designänderungen von unschätzbarem Wert ist.
Umweltfreundliche PCB-Herstellung als Wettbewerbsvorteil
Die Umweltverträglichkeit wird in der Leiterplattenfertigung zunehmend zum entscheidenden Differenzierungsmerkmal. Fortschrittliche Hersteller haben erkannt, dass nachhaltige Produktionsmethoden nicht nur ökologisch sinnvoll sind, sondern auch wirtschaftliche Vorteile bieten. Die Implementierung umweltfreundlicher Technologien führt zu Kosteneinsparungen durch reduzierten Ressourcenverbrauch und geringere Entsorgungskosten für Abfälle und Chemikalien.
Europäische Leiterplattenproduzenten haben in den letzten Jahren erhebliche Investitionen in umweltschonende Fertigungsprozesse getätigt. Dazu gehören geschlossene Wasserkreisläufe, die den Frischwasserverbrauch um bis zu 90% reduzieren, sowie energieeffiziente Anlagen, die den Stromverbrauch deutlich senken. Einige Hersteller haben bereits komplett auf erneuerbare Energien umgestellt und produzieren CO₂-neutral.
Besonders bemerkbar macht sich der Nachhaltigkeitstrend bei den eingesetzten Materialien. Die traditionelle Leiterplattenfertigung verwendet teilweise problematische Chemikalien, die durch umweltfreundlichere Alternativen ersetzt werden. So werden beispielsweise halogenfreie Basismaterialien eingesetzt, die bei der Entsorgung keine schädlichen Dioxine freisetzen. Auch bei den Lötprozessen hat sich viel getan – bleifreies Löten ist inzwischen Standard und entspricht der RoHS-Richtlinie der EU.
Nachhaltigkeit in der Leiterplattenfertigung ist keine Option mehr, sondern eine Notwendigkeit. Kunden erwarten heute umweltbewusste Produktion genauso selbstverständlich wie hohe Qualität und wettbewerbsfähige Preise.
Führende Leiterplattenhersteller gehen noch einen Schritt weiter und setzen auf eine vollständige Ökobilanzierung ihrer Produkte, die den gesamten Lebenszyklus von der Materialgewinnung bis zur Entsorgung umfasst. Diese Transparenz wird von umweltbewussten Kunden, insbesondere aus der Konsumgüterelektronik, zunehmend nachgefragt und honoriert. Der Trend zu nachhaltigen Elektronikprodukten eröffnet spezialisierten europäischen Herstellern neue Marktchancen im Wettbewerb mit Massenproduzenten aus Asien.
Auswahlkriterien für spezialisierte Leiterplattenhersteller nach Anwendungsgebiet
Die Wahl des richtigen Leiterplattenherstellers ist entscheidend für den Erfolg eines elektronischen Produkts. Je nach Anwendungsgebiet variieren die Anforderungen erheblich – von extremer Zuverlässigkeit in der Luftfahrt bis hin zu Kosteneffizienz bei Konsumgütern. Branchenspezifische Zertifizierungen spielen dabei eine zentrale Rolle, da sie die Einhaltung der relevanten Standards und Normen sicherstellen.
Die Entwicklungspartnerschaft mit dem Leiterplattenhersteller gewinnt zunehmend an Bedeutung. Ein frühzeitiger Austausch im Designprozess kann kostspielige Anpassungen in späteren Phasen vermeiden und die Time-to-Market verkürzen. Viele spezialisierte Hersteller bieten deshalb umfassende Beratungsleistungen an, die von der Materialauswahl bis hin zur fertigungsgerechten Optimierung des Layouts reichen.
Die Auswahl sollte jedoch nicht nur auf Basis technischer Kriterien erfolgen. Auch Faktoren wie Lieferzuverlässigkeit, Kommunikationskultur und geografische Nähe können entscheidend sein. Besonders bei komplexen Projekten mit häufigen Designänderungen ist eine enge und unkomplizierte Zusammenarbeit von unschätzbarem Wert. Können Sie es sich leisten, bei kritischen Projekten auf einen Hersteller zu setzen, der nicht flexibel auf kurzfristige Änderungen reagieren kann?
Automotive-Elektronik: IATF 16949-zertifizierte Hersteller für Fahrzeugelektronik
Die Automobilindustrie stellt außergewöhnlich hohe Anforderungen an elektronische Komponenten. Leiterplatten müssen extremen Temperaturschwankungen, Vibrationen und einer Lebensdauer von bis zu 15 Jahren standhalten. Die IATF 16949-Zertifizierung ist für Leiterplattenhersteller in diesem Segment unverzichtbar. Sie basiert auf der ISO 9001, geht aber mit branchenspezifischen Anforderungen deutlich darüber hinaus und setzt besonders strenge Maßstäbe bei der Prozesssicherheit und Rückverfolgbarkeit.
Führende Hersteller wie AT&S, KSG und Schweizer Electronic haben sich auf Automotive-Elektronik spezialisiert und bieten spezielle Technologien für diese Anwendungen an. Dazu gehören thermisch optimierte Substrate für Leistungselektronik, wie sie in Elektrofahrzeugen benötigt werden, sowie hochzuverlässige Verbindungstechniken für sicherheitskritische Steuergeräte. Ein typisches Beispiel ist die Integration von Dickkupferbereichen in HDI-Leiterplatten, die sowohl die Leistungselektronik als auch die Steuerelektronik auf einem einzigen Board vereinen.
Die Anforderungen an die Dokumentation sind in der Automobilindustrie besonders hoch. PPAP (Production Part Approval Process) und FMEA (Failure Mode and Effects Analysis) sind Standard. Spezialisierte Leiterplattenhersteller müssen diese Prozesse beherrschen und lückenlos dokumentieren. Die 8D-Methodik
zur systematischen Problemlösung ist bei Qualitätsabweichungen obligatorisch und erfordert entsprechende Strukturen beim Hersteller.
Medizintechnik: ISO 13485-konforme Fertigung bei Schoeller Electronics und Contag
Medizinische Geräte unterliegen strengen regulatorischen Anforderungen, die sich auch auf die verwendeten Leiterplatten erstrecken. Die ISO 13485-Zertifizierung ist speziell auf die Anforderungen von Medizinprodukteherstellern zugeschnitten und stellt sicher, dass alle Komponenten den höchsten Qualitäts- und Sicherheitsstandards entsprechen. Spezialisten wie Schoeller Electronics und Contag haben ihre Prozesse auf diese Anforderungen ausgerichtet.
Besonders kritisch in der Medizintechnik ist die Zuverlässigkeit der Leiterplatten. Ausfälle können hier im schlimmsten Fall lebensbedrohliche Konsequenzen haben. Hersteller setzen daher auf fortschrittliche Testverfahren, die weit über die Standardprüfungen hinausgehen. Dazu gehören Burn-In-Tests, bei denen die Leiterplatten über längere Zeit unter erhöhter Temperatur und Spannung betrieben werden, um potenzielle Frühausfälle zu identifizieren. Contag hat für medizintechnische Anwendungen einen speziellen Clean-Room-Bereich eingerichtet, der Kontaminationen minimiert.
Die Materialauswahl für medizintechnische Leiterplatten folgt strengen Kriterien bezüglich Biokompatibilität und chemischer Stabilität. Hersteller wie Schoeller Electronics bieten spezielle biokompatible Oberflächenbeschichtungen an, die für den direkten Kontakt mit dem menschlichen Körper geeignet sind – eine wichtige Voraussetzung für implantierbare Medizinprodukte und Sensoren. Wie bei einem chirurgischen Instrument muss auch bei der Leiterplatte absolute Zuverlässigkeit unter allen Bedingungen gewährleistet sein.
Industrieelektronik: Langzeitverfügbarkeit und Obsoleszenzmanagement nach IPC-Klasse 3
Industrielle Anwendungen stellen besondere Anforderungen an die Langzeitverfügbarkeit von Leiterplatten. Während Konsumgüter oft nur wenige Jahre im Markt sind, müssen industrielle Steuerungen und Anlagen über Jahrzehnte gewartet und repariert werden können. Spezialisierte Leiterplattenhersteller bieten daher ausgefeilte Konzepte für das Obsoleszenzmanagement an, die eine Versorgung mit kompatiblen Ersatzteilen über den gesamten Lebenszyklus der Produkte sicherstellen.
Die Fertigung nach IPC-Klasse 3, dem höchsten Standard der IPC-A-600-Norm, ist in der Industrieelektronik weit verbreitet. Diese Klasse definiert besonders strenge Kriterien für die Qualität und Zuverlässigkeit von Leiterplatten und wird für Anwendungen empfohlen, bei denen ein Ausfall schwerwiegende Konsequenzen haben könnte. Die Einhaltung dieser Standards erfordert sowohl hochwertige Materialien als auch präzise kontrollierte Fertigungsprozesse, die nicht alle Hersteller bieten können.
Besonders anspruchsvoll sind industrielle Anwendungen mit extremen Umgebungsbedingungen, wie sie etwa in der Prozessindustrie oder in Outdoor-Installationen vorkommen. Hier kommen spezielle Basismaterialien mit verbesserten thermischen und chemischen Eigenschaften zum Einsatz. Hochtemperaturbeständige Polyimid-Substrate ermöglichen Betriebstemperaturen von bis zu 260°C, während konforme Beschichtungen den Schutz vor Feuchtigkeit, Staub und aggressiven Medien gewährleisten.
Luft- und Raumfahrt: AS9100-zertifizierte Produzenten für höchste Zuverlässigkeit
Die Luft- und Raumfahrtindustrie stellt die wohl höchsten Anforderungen an die Zuverlässigkeit elektronischer Komponenten. Hier sind Fehler schlichtweg nicht tolerierbar. Die AS9100-Zertifizierung, die speziell für Lieferanten dieser Branche entwickelt wurde, geht weit über die allgemeine ISO 9001 hinaus und umfasst zusätzliche Anforderungen an Risikomanagement, Konfigurationskontrolle und Rückverfolgbarkeit.
Nur wenige europäische Leiterplattenhersteller haben diese anspruchsvolle Zertifizierung erlangt. Sie fertigen nach dem Prinzip "Zero Defect" und setzen auf umfassende Testverfahren, die jede einzelne Leiterplatte auf Herz und Nieren prüfen. Dazu gehören erweiterte elektrische Tests, Röntgeninspektionen und thermische Belastungstests. Die Ausbeute ist entsprechend niedriger als bei Standard-Produktionen, was sich in höheren Kosten niederschlägt – ein Preis, den die Kunden für die außergewöhnliche Qualität und Zuverlässigkeit zu zahlen bereit sind.
Besonders interessant für die Luft- und Raumfahrtanwendungen sind Leiterplatten mit integrierten Sensorfunktionen, die eine kontinuierliche Zustandsüberwachung ermöglichen. Diese können beispielsweise Temperaturschwankungen, Vibrationen oder Feuchtigkeit erfassen und so frühzeitig auf potenzielle Probleme hinweisen. Die Integration solcher Funktionen erfordert spezielle Designkenntnisse und Fertigungstechnologien, die nur von hochspezialisierten Herstellern beherrscht werden.
Deutsche Leiterplattenhersteller im globalen Wettbewerb
Der globale Markt für Leiterplatten ist hart umkämpft und wird volumenmäßig klar von asiatischen Herstellern dominiert. Dennoch haben sich deutsche und europäische Produzenten erfolgreich in anspruchsvollen Nischenmärkten positioniert. Statt mit den asiatischen Massenherstellern über den Preis zu konkurrieren, setzen sie auf technologische Exzellenz, Qualität und maßgeschneiderte Lösungen für anspruchsvolle Anwendungen.
Die Strategie der Spezialisierung und Differenzierung hat sich als erfolgreich erwiesen. Während der globale PCB-Markt jährlich um etwa 3-4% wächst, konnten führende deutsche Spezialisten wie Würth Elektronik und Schweizer Electronic in ihren Kernmärkten deutlich höhere Wachstumsraten erzielen. Besonders in technologisch anspruchsvollen Segmenten wie Automotive-Elektronik und Industriesteuerungen behaupten sie ihre starke Position.
Ein weiterer Erfolgsfaktor deutscher Hersteller ist die enge Verzahnung mit den lokalen Innovations-Ökosystemen. Die Zusammenarbeit mit Forschungsinstituten, Hochschulen und innovativen Startups ermöglicht ihnen den frühzeitigen Zugang zu neuen Technologien und Anwendungsfeldern. Diese Innovationsnähe ist besonders wertvoll in einem Markt, der sich durch immer kürzere Technologiezyklen auszeichnet.
Technologische Alleinstellungsmerkmale von KSG, Würth Elektronik und Schweizer Electronic
Deutsche Leiterplattenhersteller haben sich durch spezifische technologische Kompetenzen im globalen Markt positioniert. KSG beispielsweise hat sich mit seiner patentierten Einpresstechnik für Hochstrom-Anwendungen einen Namen gemacht. Diese Technologie ermöglicht die Integration von Kupfer-Inlays mit Stärken bis zu 3mm, was besonders für Leistungselektronik in E-Fahrzeugen relevant ist.
Würth Elektronik punktet mit seiner HDI-Technologie der neuesten Generation, die Strukturbreiten von unter 50µm und Aspektverhältnisse von bis zu 1:0,5 ermöglicht. Diese Präzision ist entscheidend für die Miniaturisierung moderner Elektronik. Die Kombination aus hoher Packungsdichte und exzellenter Signalintegrität macht Würth zu einem bevorzugten Partner für Highspeed-Digitalanwendungen.
Schweizer Electronic hat sich durch innovative Wärmemanagement-Lösungen differenziert. Ihre CoolLam-Technologie integriert Kühlstrukturen direkt in die Leiterplatte und erreicht damit eine bis zu 30% bessere Wärmeableitung als konventionelle Designs. Diese Kompetenz ist besonders wertvoll für Hochleistungsanwendungen in der Automobilelektronik.
Schnelllieferservice und Prototyping-Kapazitäten von Beta LAYOUT und Multi-CB
Im Bereich der Prototypenfertigung und Schnelllieferungen haben sich deutsche Anbieter durch außergewöhnliche Flexibilität und Geschwindigkeit etabliert. Beta LAYOUT kann durch vollautomatisierte Prozesse Prototypen in unter 48 Stunden liefern - ein Service, der besonders in der Entwicklungsphase neuer Produkte geschätzt wird. Die Pool-Fertigung ermöglicht dabei auch bei Kleinserien wirtschaftliche Stückkosten.
Multi-CB hat ein innovatives Fast-Track
-System entwickelt, das die parallele Bearbeitung mehrerer Kundenaufträge optimiert. Durch intelligente Produktionsplanung und modernste Fertigungsanlagen können selbst komplexe Multilayer-Designs innerhalb von 3-5 Arbeitstagen realisiert werden. Die Integration von Online-Design-Tools ermöglicht zusätzlich eine sofortige Machbarkeits- und Kostenanalyse.
Just-in-Time-Lieferung und Lagerhaltungskonzepte nach KANBAN-Prinzip
Deutsche Leiterplattenhersteller haben ausgefeilte Logistikkonzepte entwickelt, um die Anforderungen der Just-in-Time-Produktion ihrer Kunden zu erfüllen. Nach dem KANBAN-Prinzip werden Produktionslosgrößen und Lagerbestände optimal auf den Kundenbedarf abgestimmt. Elektronische KANBAN-Systeme ermöglichen eine automatische Nachproduktion, sobald definierte Mindestbestände unterschritten werden.
Die Integration in die Supply-Chain-Systeme der Kunden geht dabei weit über traditionelle Bestellprozesse hinaus. Real-time Produktions- und Versandverfolgung, automatische Bestandsmeldungen und vorausschauende Bedarfsplanung sind Standard. Diese enge Verzahnung reduziert nicht nur Lagerkosten, sondern minimiert auch das Risiko von Produktionsunterbrechungen.
Kooperationsmodelle mit asiatischen Partnerwerken nach Dual-Sourcing-Strategie
Um ihre Wettbewerbsfähigkeit zu stärken, haben viele deutsche Leiterplattenhersteller strategische Partnerschaften mit asiatischen Fertigern aufgebaut. Diese Dual-Sourcing-Strategie kombiniert die technologische Expertise und Flexibilität der deutschen Standorte mit den Kostenvorteilen asiatischer Großserienfertigung. Qualitätsstandards und Prozesse werden dabei streng harmonisiert, um gleichbleibende Produktqualität zu gewährleisten.
Die Zusammenarbeit erfolgt typischerweise nach einem hybriden Modell: Prototypen, kritische Komponenten und Eilaufträge werden in Deutschland gefertigt, während Großserien mit stabilem Design in Asien produziert werden. Deutsche Techniker sind permanent in den Partnerwerken vor Ort, um die Einhaltung der Qualitätsstandards zu überwachen und technologischen Transfer sicherzustellen.
Die Zukunft der deutschen Leiterplattenindustrie liegt nicht im Preiswettbewerb mit asiatischen Massenherstellern, sondern in der intelligenten Kombination von Technologieführerschaft, Flexibilität und strategischen Partnerschaften.